Introducing the SafeWork Platform

Every hour, an average of 38,812 occupational injuries occur worldwide. StrongArm has a mission to keep these Industrial Athletes™ proud, protected, and productive with the SafeWork Platform: ergonomic sensors, microlearning, and coaching tools to prevent workplace injuries, optimize facility performance, and instill a culture of safety.

We believe in empowering workers with the tools and knowledge necessary for a healthier, more efficient workplace—and bringing them home safely, every day.

This is why
StrongArm exists.
Pillars of SafeWork
Injury Prevention
Our SafeWork Platform combines unique data & training to prevent soft tissue injuries.


strain / sprain injuries as
compared to expected.
Proactive Safety Insights
Realtime alerting and leading indicator safety metrics give your frontline Athletes & Managers the ability to intervene early and often.
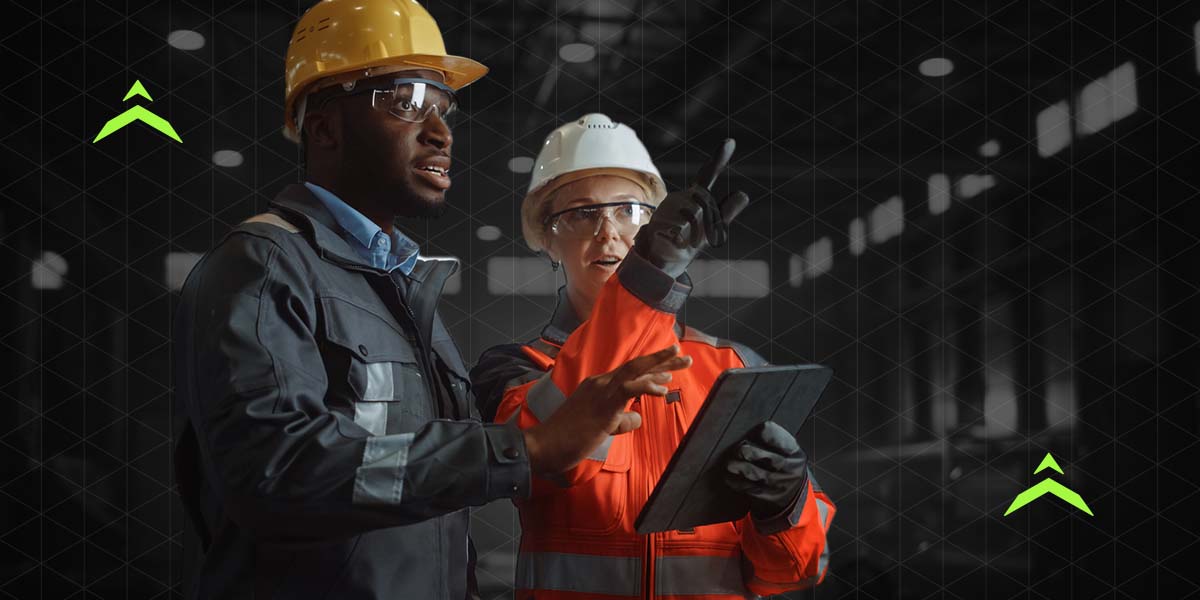

Personalized Training
Digital micro learning delivered directly to Athletes train them to apply the principles of Strong Human Movement across all job tasks.
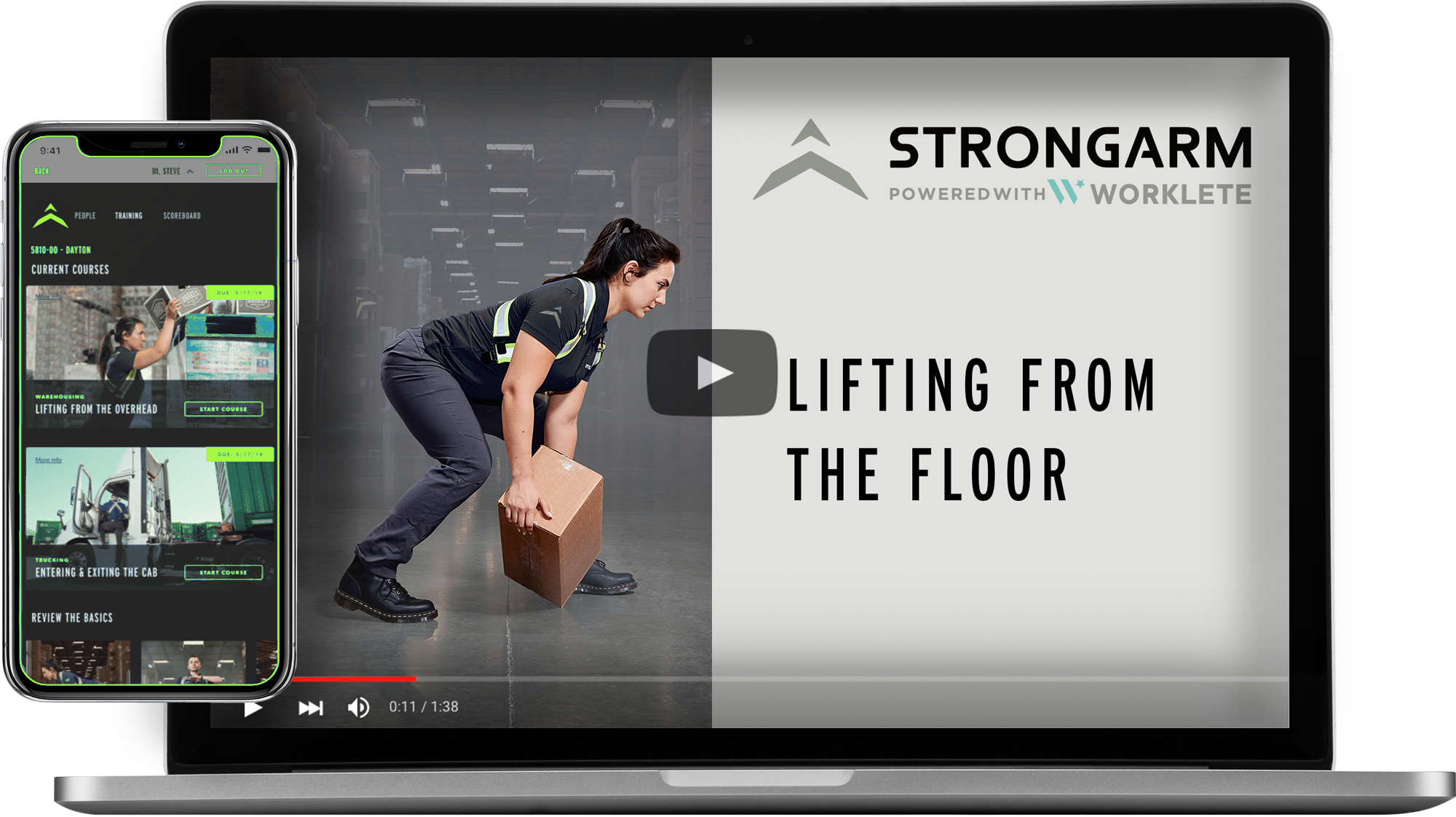

Operationalize Safety
With proactive facility, shift, job, and individual safety insights available at your fingertips, organizations can now manage safety like never before.


Made Safer by StrongArm



























